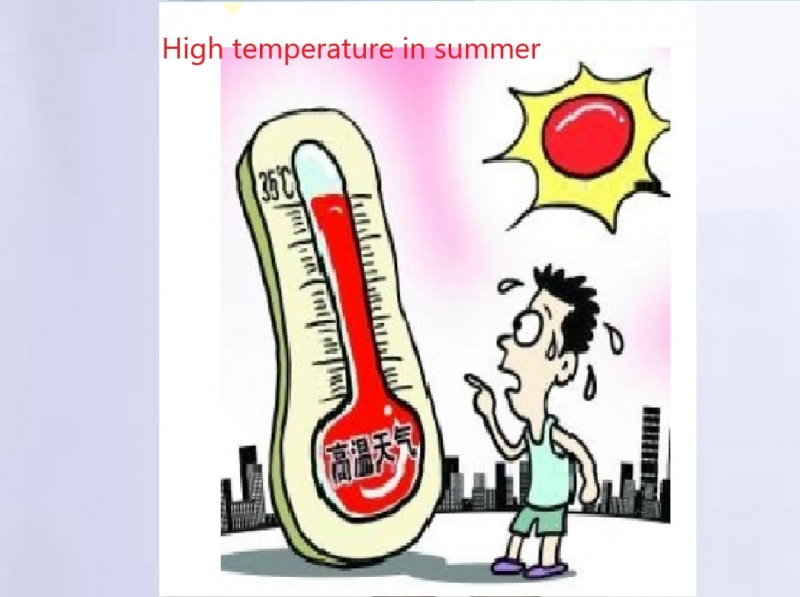
Summer is coming, how avoid sodium alginate of the decrease in viscosity?
Entering the dog days, high temperature mode is turned on all over the country. Facing the hottest time of the year, why sodium alginate viscosity may decrease and hydrolyze? How to solve it?
Effect of Temperature on Sodium Alginate viscosity
Sodium alginate is a hydrophilic colloid. Generally speaking, hydrophilic colloids have such a property that the temperature rises, and the viscosity will be affected and gradually decreased. Within a limited range, the temperature increases by about 1 degree, and the viscosity decreases by about 3%. If it is not heated for a long time, the viscosity drop is reversible, but the high temperature for a long time will cause the molecular chain of sodium alginate to break, and the viscosity drop is irreversible. The figure below shows two kinds of sodium alginate with different viscosities prepared into 5% raw paste, and the viscosity changes of the raw paste at different temperatures are compared.
It can be seen from the figure that the apparent viscosity of the original paste will continue to decrease with the increase of temperature. Therefore, the higher the temperature of the sodium alginate solution, the lower the viscosity, and the greater the loss of the viscosity of the solution.
Hydrolysis of Sodium Alginate
Hydrolysis of sodium alginate
The hydrolysis of sodium alginate generally refers to the phenomenon that the molecular chain breaks and the viscosity decreases greatly. Sodium alginate will degrade to varying degrees no matter in aqueous solution or dry powder, which is characterized by the continuous decrease of viscosity, and the constant change of average molecular mass and relative molecular mass distribution range. In addition, sodium alginate is a macromolecular organic compound extracted from nature. In summer, if it encounters bacteria and molds, it is easy to spoil and deteriorate, which will cause the solution to not be preserved for a long time and affect the use effect. The factors that lead to the hydrolysis of sodium alginate are as follows:
1. Microorganisms grow faster in hot weather, leading to hydrolysis.
2. Ultraviolet light has a significant degradation effect on sodium alginate, and the degradation of sodium alginate is more obvious in the state of dilute solution. Some experiments show that after 8 hours of simultaneous irradiation, the viscosity of 1% dilute solution decreases by about 13 times that of dry product.
3. Some oxidants, reducing agents, etc. will also cause the hydrolysis of sodium alginate.
Precautions
In response to factors such as rising temperatures in summer and accelerated microbial growth, Shandong Jiejing Group Corporation strictly controls the production process to improve product stability, appropriately increases product viscosity to offset the decrease in viscosity caused by temperature rise, and adds an appropriate amount of preservatives for anti-corrosion and sterilization.
At the same time, we also recommend that textile printing and dyeing factory can do the following in light of the actual situation:
1. Avoid strong light when storing, reduce the storage temperature, and pay attention to ventilation and heat dissipation during storage.
2. Add appropriate amount of preservative according to demand when beating.
3. Appropriate beating to avoid long-term storage of sodium alginate raw solution.
4. The beating tank and the expansion tank should be fully discharged without residual glue, and the container should be cleaned regularly, especially the cleaning of the pipeline to prevent bacteria from growing.
5. The beating time in summer can be appropriately shortened, and attention should be paid to cooling down when the temperature is too high.
6. The feeding order of urea can be adjusted, and urea can be added in a timely manner to delay the temperature rise (according to the heat absorption of urea dissolution, the temperature of the original paste can be reduced), the feeding order of baking soda can also be adjusted to shorten the time interval of adding into the pulping machine.